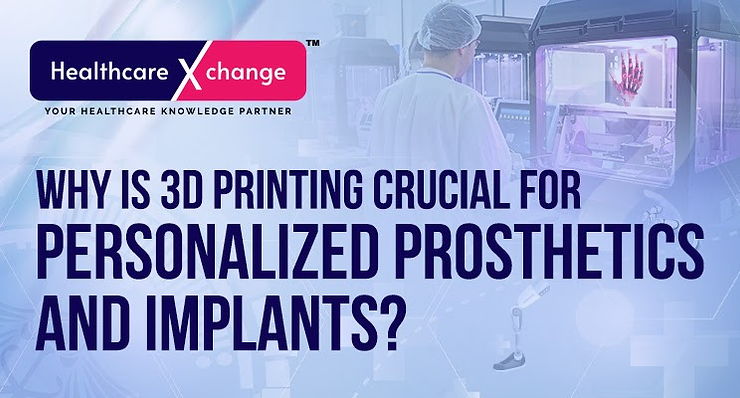
Why 3D printing is the future of patient-specific prosthetics and implants?
- Imaging and diagnostics
- October 15, 2024
Highlights
-
3D printing creates implants tailored to each patient’s needs
-
Personalised prosthetics, designed for individual anatomy, are made possible through the technique
The 3D printing sector’s rapid growth promises a bright future for personalised medical equipment such as prostheses and implants. The healthcare industry’s longstanding desire for custom gadgets is becoming a reality, thanks to recent technological advances in digital and product design approaches.
Computer-aided design and additive manufacturing, or 3D printing, have gained prominence for their ability to craft intricate devices surpassing traditional methods. This technique is flexible in design, cost-effective, and enables rapid prototyping. Elkem Silicones’ Global Business Development Manager, Karsten Schlichter, highlights the technique’s superior flexibility and diversity compared to traditional casting methods, significantly reducing the time from concept to final product by over 70%.
3D printing in prosthetics
In prosthetics, the method is poised to revolutionise customisation. Schlichter addresses the challenge of creating artificial limbs tailored to each patient’s unique needs, emphasising the importance of aligning the mechanical device with the patient’s specific size. Comfort in prosthesis and prosthetic liners is crucial for daily life, and the technique allows for more precise internal structures, offering a snug fit, enhanced shock absorption, and reduced scarring. This advancement promotes increased mobility and self-reliance.
Recent and future developments include exploring bioprinting’s potential, where human cells are incorporated into printed structures for more biocompatible implants. Additionally, 3D printing advancements enable the integration of sensors and AI into prosthetics, introducing features like haptic feedback and intuitive control, enhancing functionality and user experience.